Concrete flooring specialist completes £1m investment in premises and equipment after building solid reputation with big-brand clients
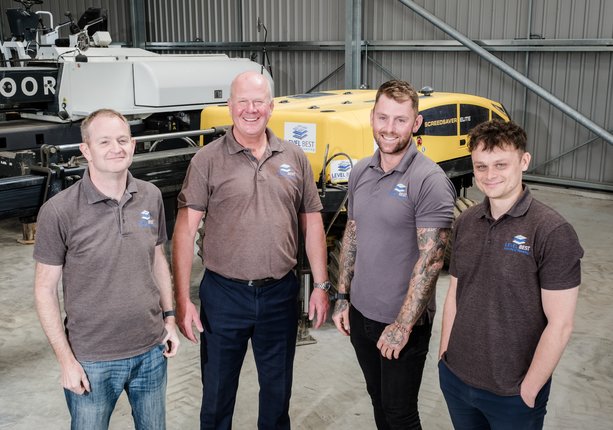
The team of four who launched Level Best Concrete Flooring in 2017. From left: Chris Wood, Jon Wilcox, Luke Morrow and Adam Brown.
A COMPANY which is installing concrete floors for major manufacturers, retailers and industrial units across the UK is building on its own solid foundations with further investment at its remote premises in East Yorkshire.
Level Best Concrete Flooring has completed the conversion of former agricultural buildings on the outskirts of Goole to provide office suites and warehouse space – including a joint-free concrete floor which showcases a new product and is the first to be installed in the UK.
The company has also added to its range of services with the purchase of a concrete crusher which has already been sent out on a mission to remove, replace and recycle – taking concrete from demolition sites and delivering an end product of fine graded AF5 aggregate direct to construction teams.
Level Best’s regular clients across the UK include a household name food retailer. In Hull, the company has installed concrete flooring at the Siemens Gamesa blade factory and at an international food production site. It’s teams are also working on new industrial units at Priory Park in Hull and at Witham in Essex.
Jon Wilcox, Managing Director of the company which he founded in 2017, said the investment will provide a platform for further growth at a business which turned over £14.5m in its last financial year.
He said: “Completion of our new facilities is an important milestone for us. I am absolutely gobsmacked with the success we have achieved and I am thoroughly looking forward to what the future will bring.
“We are extremely proud of what we have achieved as a business. When we started we could only imagine the growth and improvements which have taken our workplace forward over the past eight years.”
Jon was joined by colleagues Adam Brown, Luke Morrow and Chris Wood in setting up Level Best Concrete Flooring in a portable cabin on a friend’s farm at Balkholme, near Howden. As business picked up they moved across the River Ouse to Swinefleet Common, riding out the losses inflicted by the pandemic and bouncing back with innovation and determination.
The plan to focus on the dilapidations market was a success, and over the years Jon increased his workforce to 12 in the head office plus the wider team of two operations managers, six supervisors and 44 site operatives working at locations across the country.
Level Best’s new warehouse at Swinefleet Common can house an expanding fleet of equipment including six laser screeds which ensure an accurate, level finish, 20 power floats used for smoothing and polishing, and 12 grinding machines in demand from customers choosing floor refurbishment over replacement.
Jon said: “It’s rare for the machinery to be in our warehouse. It just moves from site to site, from one job to the next. A lot of our equipment never comes back!”
The business growth has come from offering additional services, and in particular solutions for clients eager to manage costs.
Jon said: “Land is very expensive to buy and in and around the major cities it’s far cheaper to refurbish existing units. It’s also quicker and more sustainable.
“The new crushing machine brings greater sustainability in terms of enabling us to offer a one-stop shop. It’s reduced our carbon footprint and it gives our customers greater assurance that we are managing everything safely. It’s been tested on a local farm yard and it’s just gone out on its first commercial job.
“We got into joint-free flooring after it was mentioned by one of our suppliers. It’s much lower maintenance because the joints are the things that usually go first. It’s got great potential in food production and storage because it helps to raise hygiene standards by not having cracks, and it all adds up to less down-time.
“The one in our new warehouse is the first to be installed in the UK. It only took us a day, and people are welcome to have a look! Overall it’s taken a year to complete the civil engineering, warehouse and offices. It represents a £1m investment and it gives us something specific to our needs – a lot more office and warehouse accommodation which is space that we will grow into.”